Adhesives for advertising, part 2
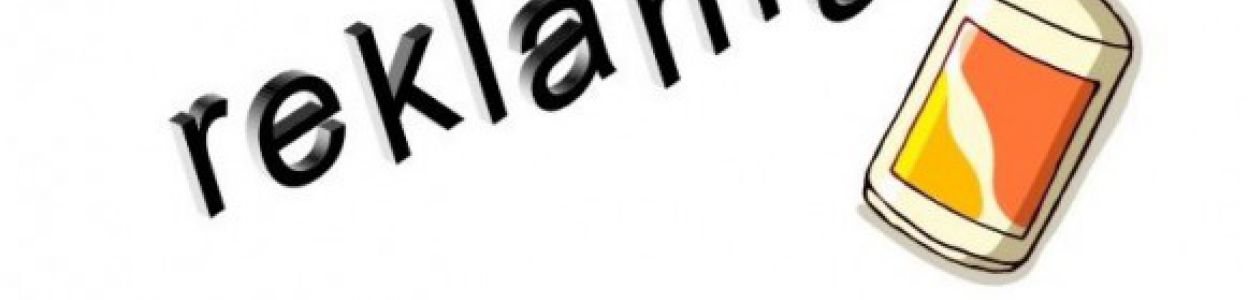
Which adhesives for advertising should be used depending on the situation? - part 2
Bonding coffers, brackets and other structural elements that will later be powder coated.
As is known, the adhesive lasts approx. 30 minutes when powder coating. must withstand 180 degrees of paint burnout. For this we use the tried and tested Acralock SA 1-15 for years. Regardless of whether we will glue steel or aluminum profiles, we use this glue without any primers. Degrease the surfaces with isopropyl alcohol or acetone and then wipe with an AP1 primer, which will eventually degrease the surface and remove the final dirt. We put the glue and put the whole thing together so that the pressure is not too big and the glue remains between the surfaces. If a gap is required, we use spacer balls.
We gain a lot of time here in relation to welding because we do not have to grind the welds later and most importantly, the surface after painting is aesthetic because the joints are not visible. Currently there is (at the time of writing this article) one more glue that can be used, i.e. ATK EP 61 with the addition of spacer balls.
Gluing plexiglass and polycarbonate - stands, boxes, showcases, drawers and other containers.
Here the matter is very simple. We use, for example, the "old technology" of ATK PMMA 4 and 16 solvent adhesives - thin and dense version. The principle is simple: medium-folded surfaces, i.e. gaps up to 0.1-0.2mm - use PMMA 16, with folds, we glue PMMA 4. Even though the initial setting is about 10-15 minutes. that's the full minimum. 24 hours and in the case of dense and larger gaps up to 48 hours. However, there is a better method: joining these materials using ATK UV 10 and 16.
ATK UV 10 - thick, to be applied even on sloping surfaces.
ATK UV 16 - rare, flows between surfaces - the so-called capillary rise.
If the glue is cured with UV light, you need a lamp - no problem, we have tested lamps with the cost of a 90 cm long fluorescent lamp - it is only ... PLN 200. We can also use a 3W or 5W flashlight to pre-fix the glue in 5 seconds. See all UV lamps.
Full cure is dependent on plexiglass / polycarbonate but takes only 10-30 seconds. and hello is already suitable for further activities.
Important - a few notes:
- When gluing with solvent-based adhesives, plexiglass will have micro-cracks even after milling, and even a few millimeters in the case of laser ones. When using uv glue when milling, they do not work out, with laser cutting only minimally, you should always carry out tests on the specific plexiglass you use.
- After cutting with a cutter / saw, we do not heat and sand the edges, there is no need to glue the edge with the glue and it will hold more firmly.
Gluing and repairing of all kinds of statuettes, ornaments and glass cases.
Currently, statuettes come from China more and more often, later we engrave them, but they often come to the point that they come off - glass or stone base and then the easiest and aesthetic way is to glue them with ATK UV 20 or ATK UV 22 glue, i.e. a rare or medium version in depending on the surface. The surface is perfectly transparent after gluing, and curing with the flashlight or a stationary lamp tested by us takes several to several seconds. In this way, we glue and repair trophies, broken elements in stands, gluing fasteners and metal hinges in showcases, and broken elements of trophies.
Sticking and production of statuettes and cups from other materials.
Here, the multitude of materials that we use is very large, but we use glue literally 2-3 pieces.
The materials that we need to glue and the glue cannot be visible - it will be transparent so that it will be as little visible as possible when it flows out - for this we use ATK PU CLEAR. We recommend it for all materials such as wood, dibond, metals including stainless steel and aluminum, natural stone including crystals. The use is very easy, because we get the glue in 50 ml cartridges, on which we put the mixer-stirrer and apply the glue wherever we need, remembering that it should not take more than 1-2 minutes from application to pressing and positioning.
Important: the glue is perfectly transparent between the surfaces and the reflux too.
In the case of surfaces where the greatest possible holding force is more important, then for surfaces such as steel, stainless steel, high-gloss steel, raw aluminum, anodized and powder coated, plexiglass, foamed pvc, abs, pc-polycarbonate, etc., we use Acralock SA 1-15, If, on the other hand, it is copper, brass, bronze, stone, wood and plastics, then we choose ATK EP 61. These are construction adhesives that have such high strength that when tearing, the material is often damaged, so we can replace them with less aesthetic and time-consuming welding riveting and welding - we will avoid further additional treatments.
Gluing banners or welding.
JIf we have several or a dozen or so banners per month, we choose ATK B170 glue. The connection is then durable and as strong as welding. In the case of large quantities, then we have a choice of manual Bosite-D or even better Bosite-DL - in fact, it must always be manual, even if we have enough work to buy an automatic banner welding machine little dog.
Important:
1. Never use double-sided tapes (even the "specialized dedicated" ones) supposedly for sticking banners - they don't work - even if the banner is indoors, it is only a matter of time until the tape starts to peel off, not to mention when the banner is outside. It's a pity you would lose customers because of this.
2. Never buy cheap automatic and manual welders - equipment for work and earning must cost its own: manual costs about 1000-1500 PLN, a good machine costs about 9000 PLN. How do they differ from the cheap ones? - After heating, they maintain their temperature as you set and this is the most important advantage of good equipment, besides durability and comfort of work on such equipment.
Pouring convex stickers - 3D so-called doming
Here the proven ATK PU 45 CLR resin. You can find cheaper epoxy resins on the market, unfortunately the sticker is very stiff after pouring and most importantly - it is not resistant to UV light. You can also find resins cured with UV light - here the problem is the high price, several times higher than the polyurethane one, and additionally we have to use expensive UV lamps that reduce profitability even further. In the end, the customer will choose another company that offers him a good and cheap 3D sticker.
Comments